Hybrid injection molding machine
Multipower H/HE
MULTIPOWER is a highly innovative product that combines optimal versatility and high performance with maximum energy savings over 50%.
Desideri saperne di più su come i nostri prodotti possono migliorare la tua produzione?
Richiedi maggiori informazioni oggi stesso e scopri come Plastic Metal può aiutarti a raggiungere risultati straordinari.
Hybrid injection molding machine
HIGH PERFORMANCE AND ENERGY SAVING
Available in the range from 50 to 800 tons, Multipower is based on a mixed technology of drives, hydraulic and electric systems, targeted to provide maximum performance with minimum power consumption.
INJECTION AXIS AND ACCUMULATORS
The injection movement is based on a rotary piston, hydraulically balanced under accumulators without any thrust bearings. This is the most complex movement of the machine and it determines the quality of the moulded product.
A servo valve (Moog) provides closed loop control of speed, pressure and backpressure thus ensuring optimal conditions even for the more sophisticated mouldings. A pump located under the injection unit, with internal gear driven by an electric motor of a very small size, provides for the recharge of the accumulators. Once the required level has been reached, the motors shuts off to minimize power consumption. Switching on/off is controlled by inverter, thus maximizing the efficiency of the system.
This procedure allows to obtain speed performance otherwise impossible and a control of a hold-on pressure extremely precise and adjustable according to the characteristics of the moulded product, reducing at the same time consumption of energy. Therefore the advantages of this application are: reliability, high performance, high precision and energy savings.
Advantages of Multipower H-HE

Maximum system reliability

Injection by rotary piston

5 point toggle clamping system

Innovative Hybrid Energy Saving technology

Guaranteed energy savings
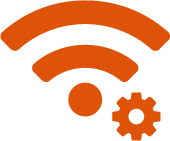
Wireless connection for on-line assistance
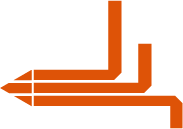
Simultaneous movements
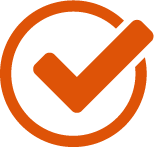
User friendly interface, simple and intuitive
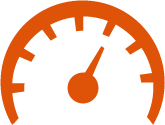
Maximum flexibility for high speed
Movements
The screw rotation of the screw is operated by an electric motor – “torque” type, directly connected and resistant to the highest mechanical stress. This brushless motor with high torque and low rpm, eliminates the negative return of belt and gear reduction systems. The motor “torque” (Baumüller), water cooled, is operated by a drive that allows to use only and exclusively the energy required by the plasticizing screw during dosing phase. It also allows to overlap all movements.
The injection movement is performed by two hydraulic cylinders which allow the unit to maintain its position thus reducing energy consumption to virtually zero. Once the system has been loaded, a non-return valve prevents the emptying of the cylinders.
Ejection can be operated by an hydraulic or electric drive. The ejection actuated by a hydraulic drive, allows a considerable ejection force and long strokes as well as high flexibility when hooking-up the ejection rods of the mould.
The mechanical structure of the clamping unit is characterized by a 5-point double toggle with steel links and special bronze bushings and a multiple point lubrication system with programmable cycles and safety devices.
The mechanical structure of the clamping unit is characterized by a 5-point double toggle with steel links and special bronze bushings and a multiple point lubrication system with programmable cycles and safety devices. The opening/closing movement is performed by an electromechanical axis that exploits a ball screw. The rotation of the system is provided by a brushless motor specially designed with a hollow shaft installed directly on axis. The motor, developed in cooperation with Moog, provides the system with torque and speed that result in a very fast and precise mould movement , perfectly controlled in acceleration and braking. At the same time it ensures an excellent control of “ mould safe”. The lubrication of the ball screw is entrusted to a special pump, with recovery of lubrication oil. The water cooled motor is also monitored by thermal sensors that control and ensure the optimal temperature of the whole system.
The opening/closing movement is actuated by a hydraulic piston that ensures reliability of the system. The movable platen is supported by adjustable sliding blocks that ensure complete safety of the mould.
An operator interface mixed with video touch and push buttons for manual operation allows a user friendly man-machine interface in a simple and intuitive way. A special option allows the operator to choose among three operation modes: “Normal”, “Eco” and “Fast”. In the first case the machine works with standard values as per our catalogues, while in “Eco” mode the system optimizes the reduction pressure of accumulators recharge in order to minimize consumption. With the option “Fast” the machine, while remaining in operation with reduced consumption, automatically sets up all the calibration conditions so as to provide the best possible performance.
REQUEST MORE INFO
Fill in the form, we’ll answer as soon as possible.