Two-platen injection moulding machine
Duo H
The DUO machines are suitable for large-size parts.
Thanks to the careful design and the customization with special equipment, the DUO model is particularly successful in the production of large-size items for the automotive industry, design, furniture and lighting.
Desideri saperne di più su come i nostri prodotti possono migliorare la tua produzione?
Richiedi maggiori informazioni oggi stesso e scopri come Plastic Metal può aiutarti a raggiungere risultati straordinari.
Two-platen injection machine
A line of two-platen injection machines suitable for the production of deep profile parts and big containers, thanks to the wide opening stroke. The special compact design allows maximum performance in the smallest space. Tie bars guided back and forth and completely independent from the moving platen movement. Locking nuts embedded in the fixed platen to ensure reliability during the locking action.
Generously dimensioned platen ejector with simultaneous ejection and mould opening. Screw rotation operated by hydraulic motor in the standard version and electric motor for the Multipower version (on request). Injection actuated by two pistons parallel and symmetric to the injection unit. Hydraulic system based on double pumps and inverter controls that allow energy savings up to 40%.
Advantages of Duo H

Maximum system reliability

Guaranteed energy savings
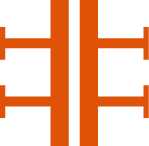
Two-platen clamping system
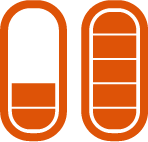
Accumulators for injection unit (H version)
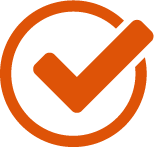
User friendly interface, simple and intuitive
The movements
Screw rotation is operated by a brushless type, water-cooled electric motor, that controls a parallel shaft gear reducer of high construction, thus reducing pressure losses and noise to a minimum. The high torque generated allows high plasticizing capacities of all plastic materials processed including “hard” types. The drive command enables to use only the energy required by the plasticizing screw during the dosing process and to overlap the movement.
The injection movement, hydraulically operated, allows to develop considerable power appropriate to the size of the machine, with very high speed. This is the most complex movement of the machine and determines the quality of the final product. The axis control, entrusted to a servo valve (Moog) in close loop control of speed, pressure and back-pressure, ensures the optimization of all the conditions required even in the most sophisticated moulding processes.
The injection movement is performed by two hydraulic cylinders which allow the unit to maintain its position thus reducing energy consumption to virtually zero. Once the system has been loaded, a non-return valve prevents the emptying of the cylinders.
Una volta caricato il sistema, una valvola di non ritorno impedisce lo svuotamento dei cilindri.
The central ejection is actuated by a hydraulic drive, allowing a considerable ejection force and long strokes as well as high flexibility when hooking-up the ejection rods of the mould. Ejection can be overlapped with mould opening. The proportional direction.
Heavy duty, compact two-platen clamp system, for fast mould changes through the automatic mould height adjustment function. The hydraulic control system is operated by a servo pump that controls and modulates the movement for high energy savings until the complete shutdown of the motor when the movement is finished. The tie bars, guided both front and rear, independently of the moving platen stroke, ensure precision of movement and fast locking action. The locking nuts are embedded in the fixed platen to guarantee high reliability during the locking action and to keep the operating area clear.
A pump located under the injection unit, with internal gear driven by an electric motor of very small size, provides for the recharge of the accumulators. The accumulators act as “energy dam” : once the required filling level has been reached the motor shuts off to minimize power consumption. The motor is controlled by a dedicated inverter thus maximizing the efficiency of the system. This system allows speed performance on the injection axis otherwise impossible and the possibility of overlapping ejection and core pullers to all other movements for faster cycles. The advantages of this application are: reliability, high performance, high precision, energy savings, flexibility of the system.
An operator interface mixed with video touch and push buttons for manual operation allows a user friendly man-machine interface in a simple and intuitive way.
REQUEST MORE INFO
Fill in the form, we’ll answer as soon as possible.